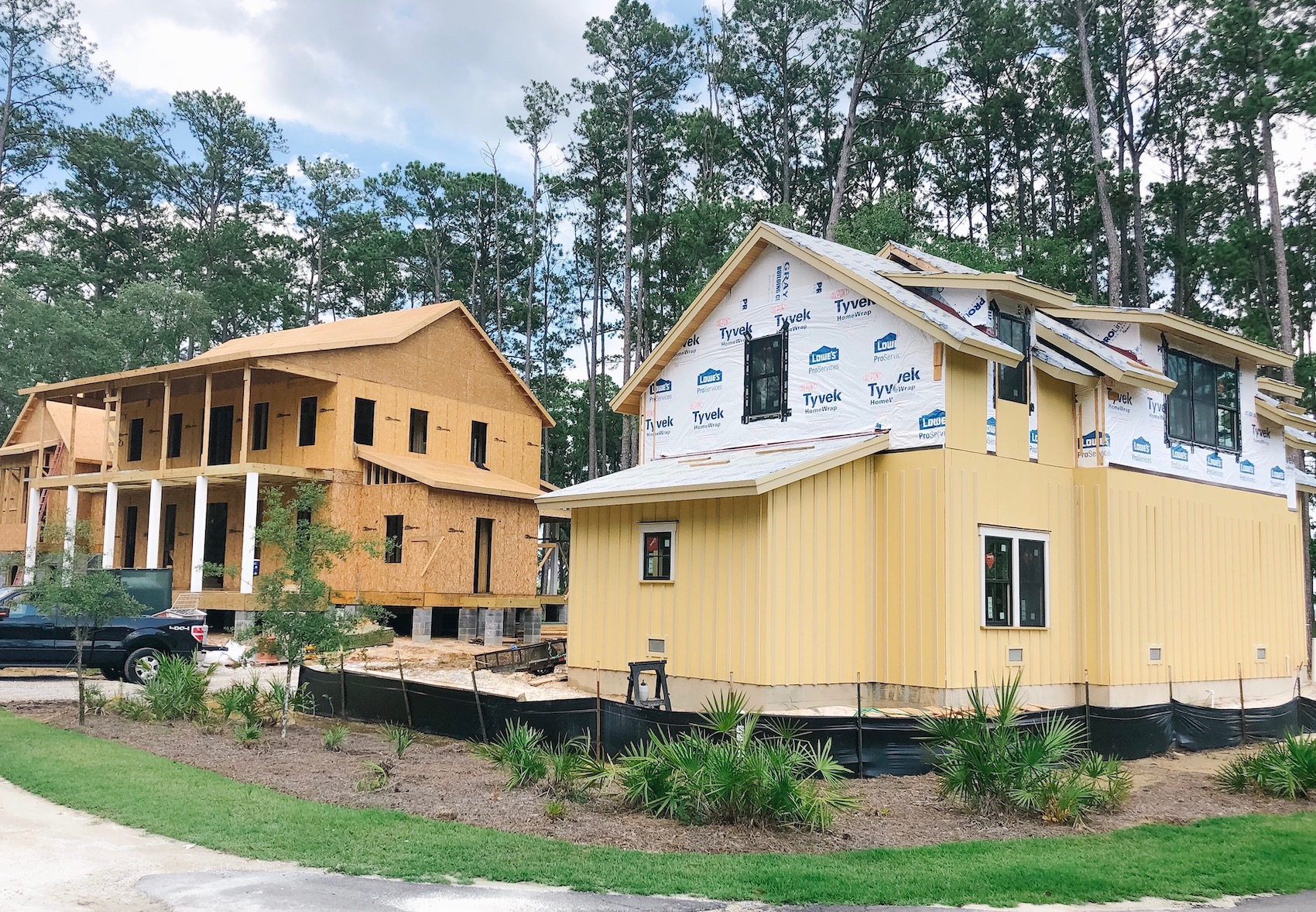
Garage/Carriage House
At this build site, the project consists of two structures; each has its own construction permit. The Garage/Carriage House was the first structure to start the build and the most advanced in progress. It is dried-in (always a good stage), the HVAC, plumbing and electrical rough-in are completed. Sheeting, siding, strapping, rough-in and framing inspections all have been passed. The windows are installed, siding is completed and ready for paint. Internally we have completed sheetrock installation in the living space, and we finished internal pine plank siding, replicating the look and feel of “barn meets industrial, ” in all other areas of the garage space. It’s pretty well advanced now, and painting will get underway next.
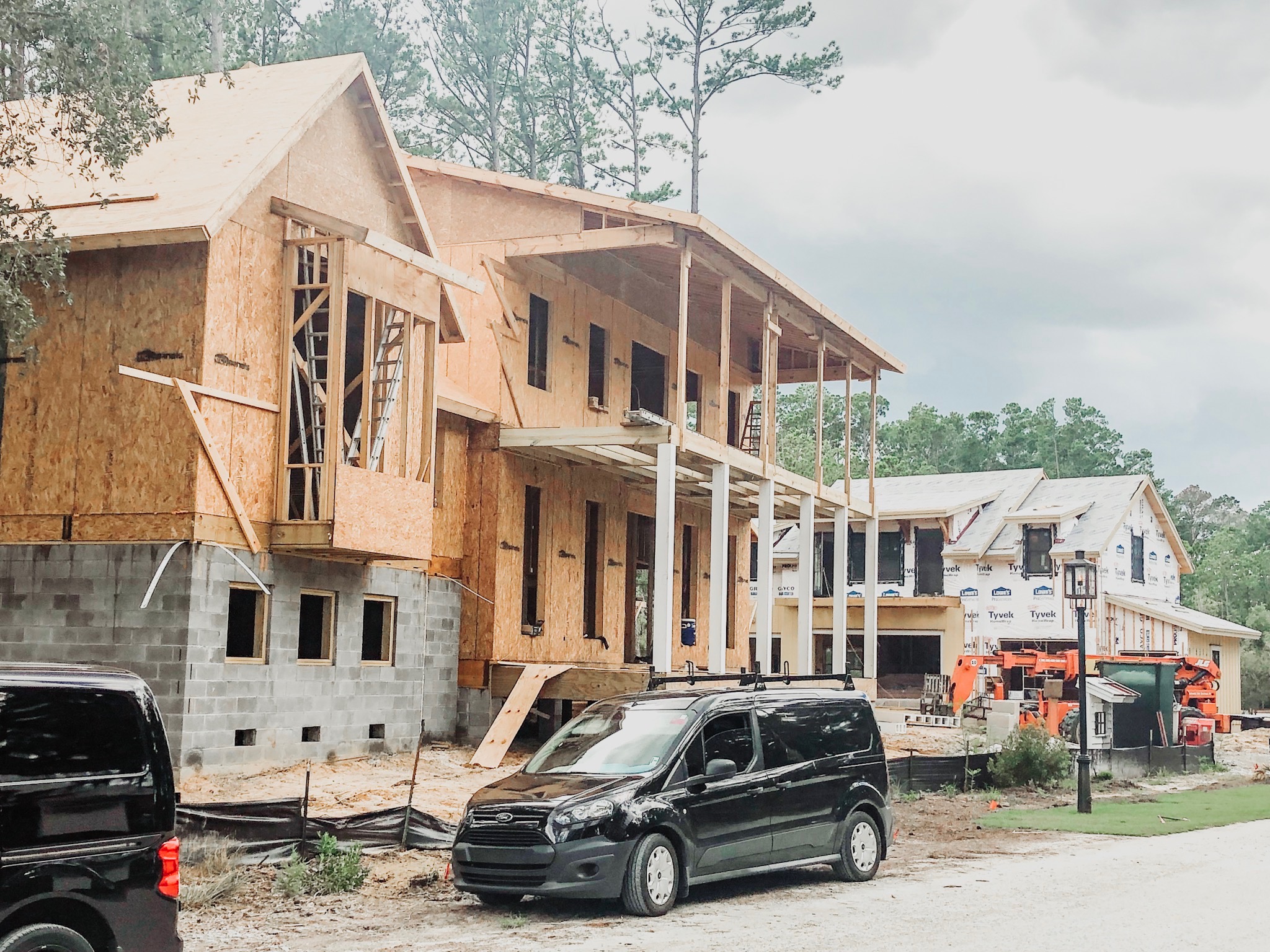
So what have been the highlights of this? Firstly working on site with such a large covered storage area has made the staging of materials a breeze. We have been able to get out of the noon sun and store both materials and equipment on a good concrete floor out of the rain. We also had a chance to express a little of our construction “art. ” The inside of the garage space is covered with either wide plank longleaf southern pine in rough cut, board-and-batten or corrugated iron for a distressed “industrial ” look. Aging new shiny corrugated sheeting from Lowes ($12 per sheet) was a process of spraying it with strong Muriatic Acid to locally strip the galvanize zinc then wetting it with seawater from the May River and letting time and nature take its course. To me, it has the look of 50-year-old barn siding but the cost is less than sheetrock! We also found a source of Cedar barn siding aged by exposure over many years. Long, wide shiplap boards were attached horizontally in the entrance hall and highlighted by timber frame elements repurposed from old Victorian floor joists. We even snuck in a faux wind brace, morticed, tenoned and pinned in an exact fashion. Not an expensive upgrade except for a little care but the effect is like nothing else in Palmetto Bluff.
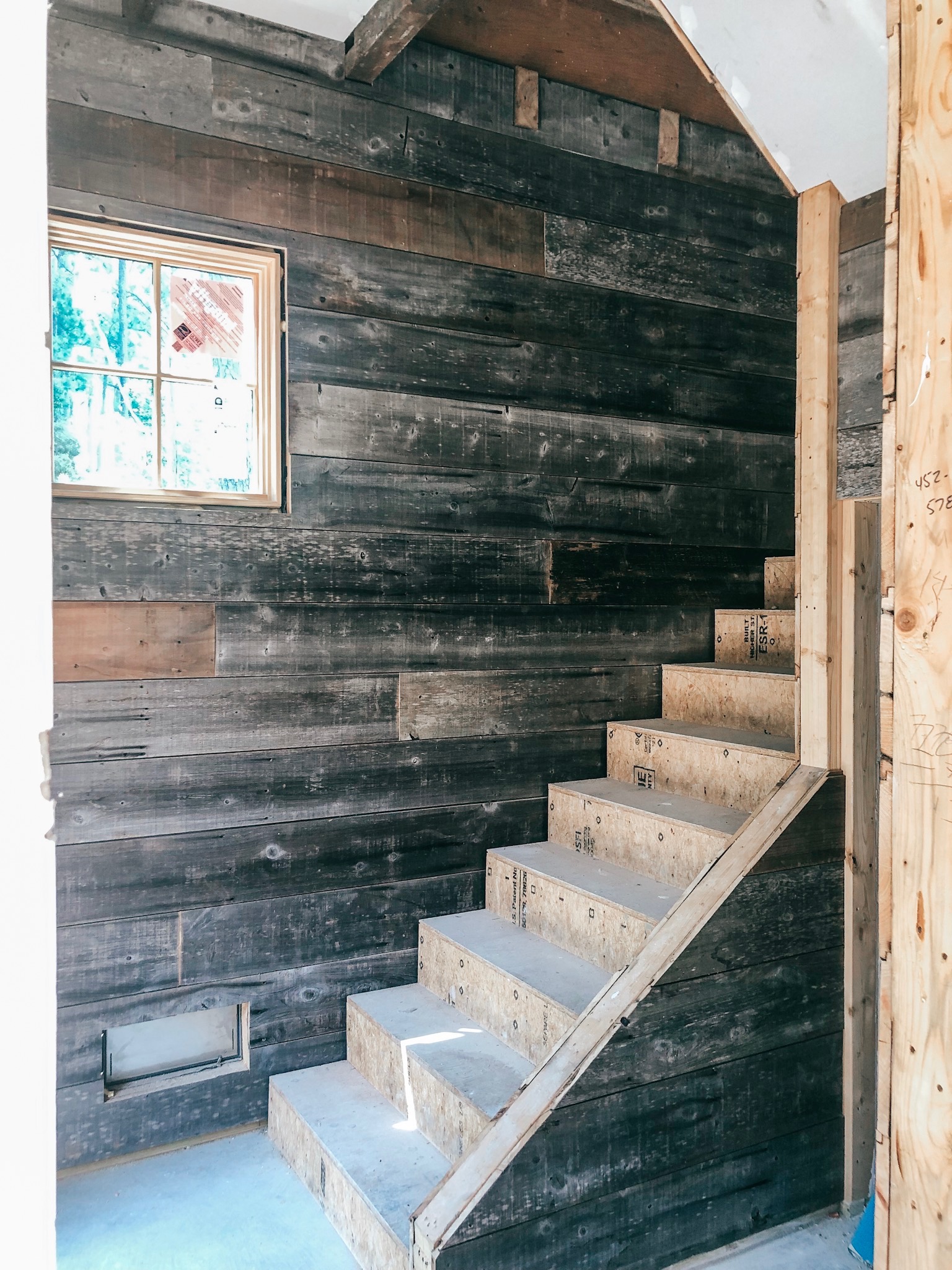
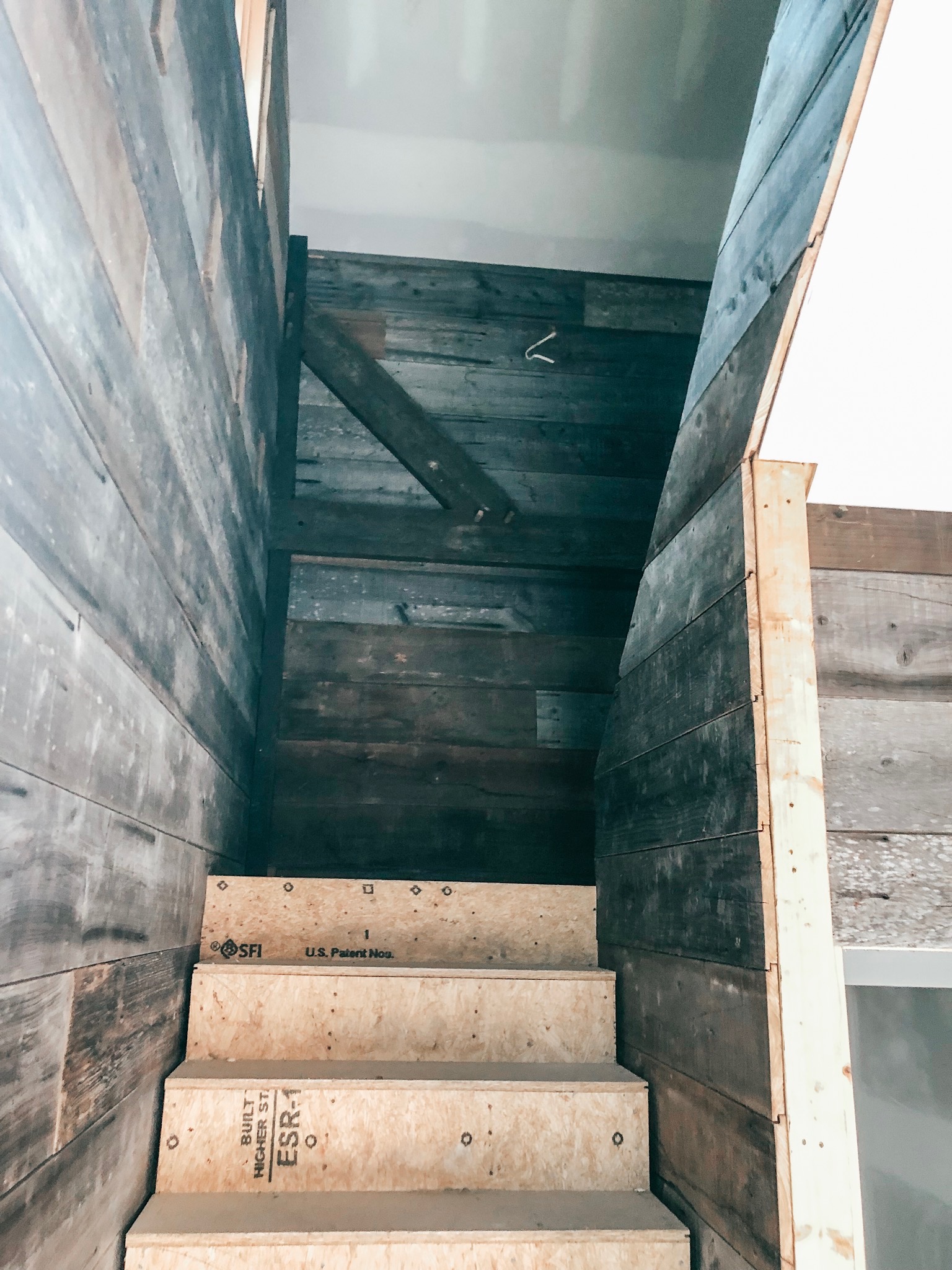
Main House
The main house started about a month after the Carriage House. 3500 sq. ft. with 2000 sq. feet of piazza space. That is now dried in (in the recent storms we had 2 inches of water on the floors, which is one reason for selecting engineered subfloor products that can withstand such a douse during construction). Now that it is dried in, plumbing and electrical rough-in are underway. We have made a few internal changes to the layout to increase the usable bedroom space with an eye to maximizing the function for vacation rental use and removed a chimney that was neither visible from the street nor needed, since we have a ventless gas fireplace in the main room. The cost savings are significant and will help counter overruns elsewhere.
The last recent highlight for us was the delivery of some serious woodworking machinery. What sort of a man does not like big expensive tools? In truth, the logic was that for sourcing 4500 square feet of 60 year-old, rough cut flooring at $4/sq. ft. more than justified the cost of this machinery to process the flooring. It will go down as skip-planed barn board, 10 “-12 “-14 “wide, glued and face-nailed to the subfloor. That calls for both a planer and a jointer.
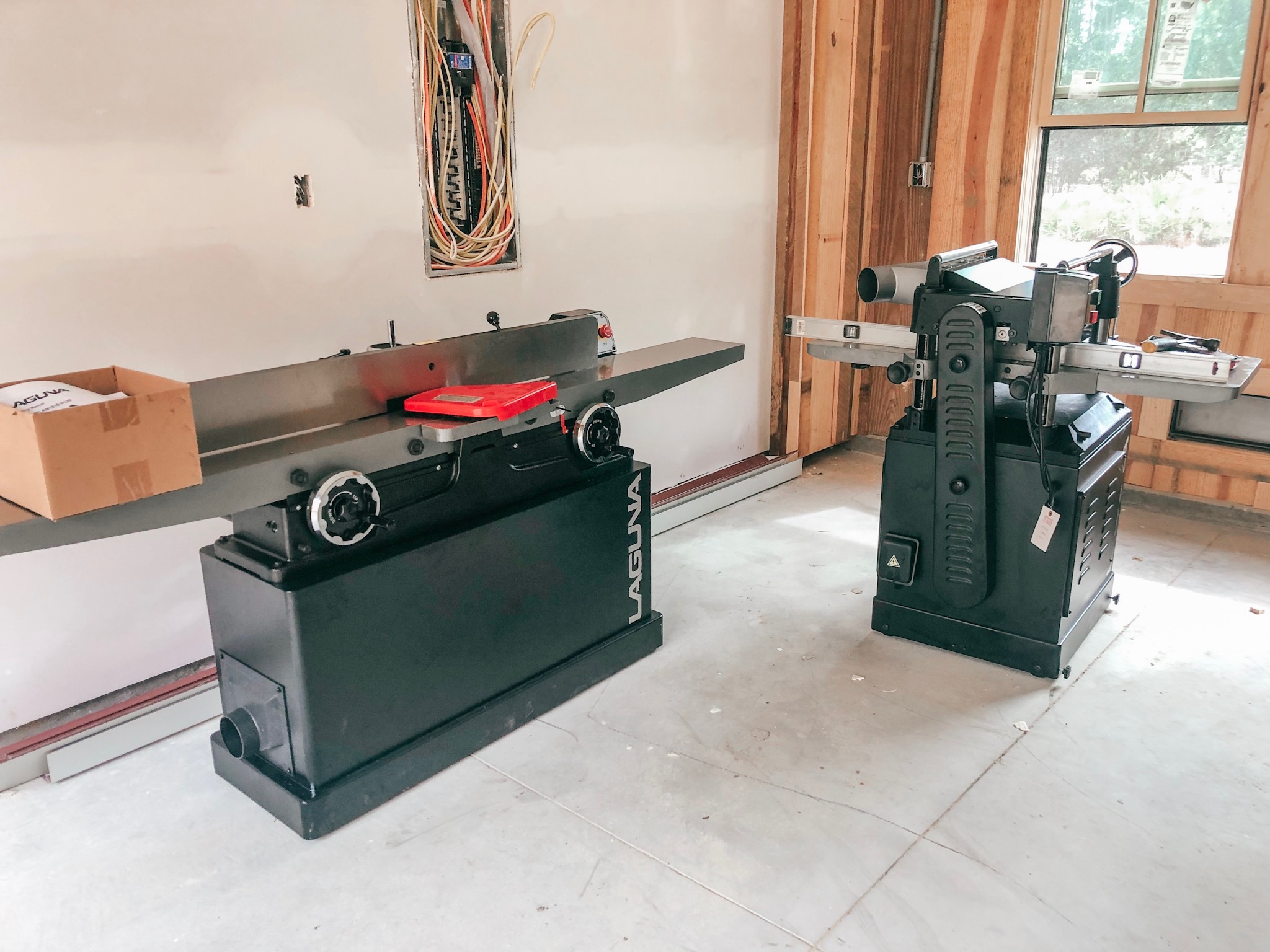
We wired them up to the temporary 220V power pole at the site and spent an hour making a 4′ high pile of shavings processing all remaining pine board-and-batten into something a bit more refined (and uniformly 19/32 thick) for walls in the main house. Red Oak, 8 ” and 10 “, 5/4 boards for the Carriage House will be next, seriously good fun to process.
Building in Palmetto Bluff will never be a low-cost exercise. However, it does not need to be wasteful of resources or prohibitively long. By careful planning and materials selection, by spending time and resources on the structure and where the eye falls, by caring for waste and working closely with all your subcontractors, it is possible to achieve a very great deal at modest cost and a great timeline.
I hope you enjoy this Blog series. Click on previous blogs below to follow the series along from the beginning:
Building in Palmetto Bluff: A Quick Pace and Managing the Timeline
Palmetto Bluff: Site Preparationand SIPS Panels Delivered
Palmetto Bluff: How to Finance and Build for Cash Flow
Palmetto Bluff: The Building of a Dream Home Begins
Custom Home Building in Palmetto Bluff
The Allure of Palmetto Bluff – Just 90 Minutes from Charleston
Palmetto Bluff: A Real Estate Investment in Vacation Rental
Interested in following this project as in progresses in real time? Be sure to sign up for our blog! Ask any questions you may have or come for a visit and see the build up-close …we’d be happy to show you how it all happens.